MIG 250 Welding: A Comprehensive Guide for Electricity Suppliers
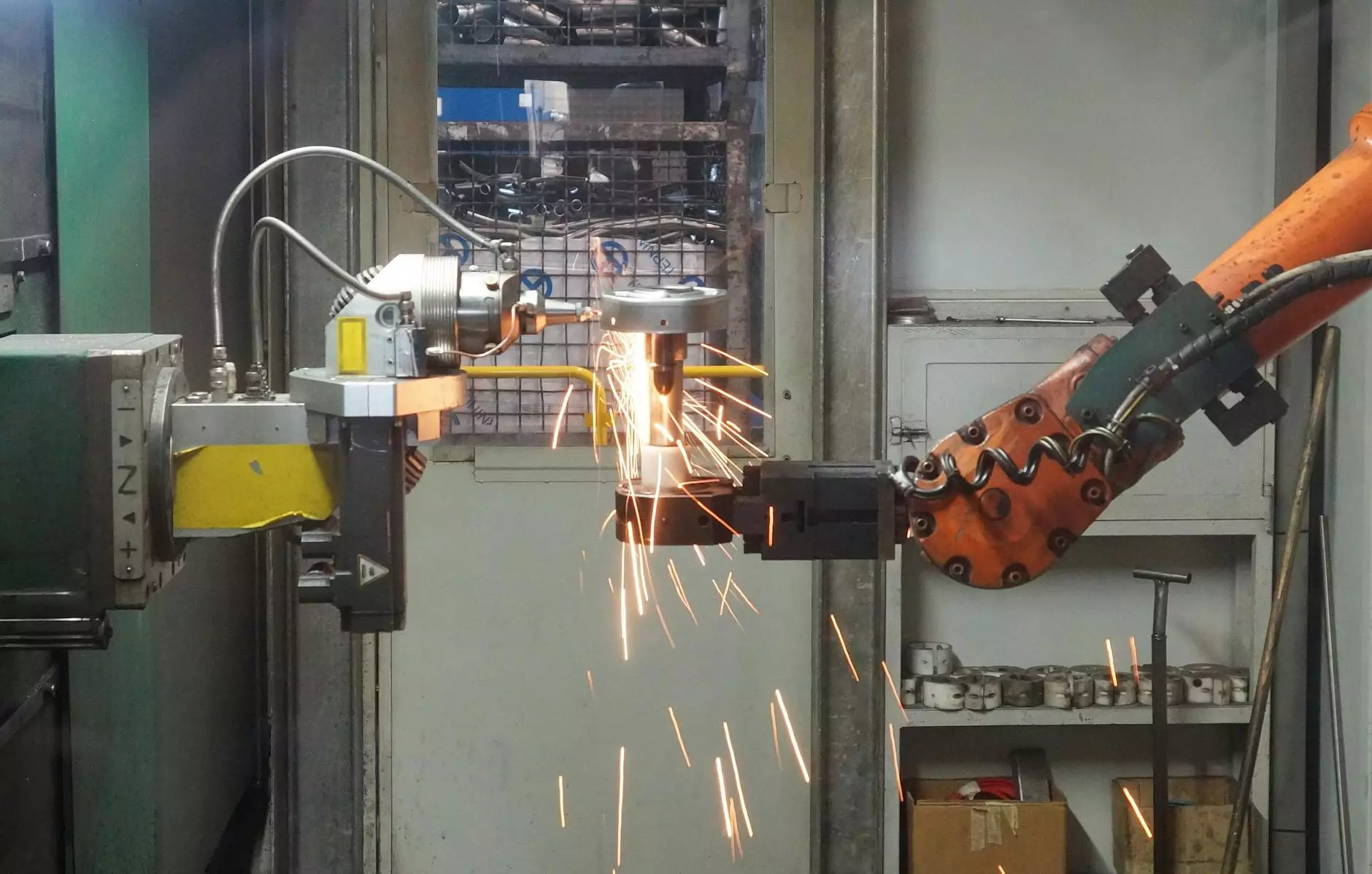
Introduction to MIG 250 Welding Technology
The MIG 250 welding machine has emerged as a highly efficient tool in the field of welding, especially for businesses like electricity suppliers. This system utilizes the Metal Inert Gas (MIG) welding process, which is favorable for various applications due to its ease of use and versatility.
Understanding the fundamentals of MIG welding is essential for suppliers looking to implement advanced manufacturing techniques. This article dives deep into the specifications and advantages of the MIG 250, along with its implications for electricity suppliers.
Understanding MIG Welding
MIG welding is a type of welding process that uses a continuous wire filament and an inert gas to create a stable arc. This method is widely used due to its efficiency and ability to create strong, clean welds. The MIG 250 model is specifically designed for both novice and seasoned welders, making it an excellent choice for electricity suppliers handling diverse welding tasks.
Advantages of MIG Welding
- Speed: MIG welding is faster than other traditional welding methods, allowing for greater productivity.
- Ease of Use: The process is easier to learn, making it perfect for beginners and experienced welders alike.
- Versatility: It can be used for a variety of materials, including aluminum, steel, and magnesium.
- Less Cleanup: The process produces less slag and spatter, reducing post-weld cleanup.
Technical Specifications of the MIG 250
The MIG 250 welding machine offers a variety of technical specifications that cater to different welding requirements:
- Power Supply: Suitable for input voltages ranging from 220V to 240V.
- Welding Current: Adjustable output from 30A to 250A, enabling versatility for various thicknesses.
- Welding Thickness: Capable of welding materials up to 1/2 inch thick.
- Wire Diameter: Uses wire from 0.8mm to 1.2mm for optimal performance.
- Efficiency: Features a high duty cycle that enhances operational efficiency and prevents overheating.
Applications of the MIG 250 in Electrical Supply
For electricity suppliers, the MIG 250 welding machine provides significant benefits, including:
1. Manufacturing Electrical Components
The MIG 250 can be used to fabricate electrical components that require precise and durable welds. Whether assembling metal enclosures or connecting conductive pathways, the MIG welding method guarantees high-quality results.
2. Repairing Electrical Equipment
In the electricity supply industry, equipment can often sustain damage or wear over time. The MIG 250 is beneficial for repairing these components, ensuring minimal downtime and reduced costs associated with replacement.
3. Structural Fabrication
Structures such as pylons and frames that support electrical systems can be fabricated using the MIG 250. Its ability to produce strong, reliable welds makes it ideal for building and maintaining infrastructure.
4. Custom Projects
Electricity suppliers often undertake custom projects. The flexibility of the MIG 250 allows for the quick adaptation to unique needs and specifications, enhancing project fulfillment.
Choosing the Right Accessories for MIG 250
To fully utilize the MIG 250 welding machine, it is important to choose the right accessories and equipment:
- Protective Gear: Always prioritize safety by using appropriate protective gear such as helmets, gloves, and clothing.
- Gas Supply: Ensure access to suitable inert gases like Argon or CO2 to enhance the welding process.
- Wire Feeders: Select compatible wire feeders that ensure a smooth and consistent wire supply.
- Cleaning Tools: Use cleaning brushes and grinders to prepare surfaces for optimal welding quality.
Maintenance Tips for MIG 250 Welding Machines
To extend the lifespan and performance of the MIG 250, regular maintenance is crucial:
- Clean the Welding Gun: Regularly checking and cleaning the welding gun helps prevent clogs and ensures smooth operation.
- Inspect the Cables: Regularly examine cables for any signs of wear or damage and replace if necessary.
- Check Gas Supply: Ensure that the gas supply is adequate and free from contaminants.
- Calibrate Settings: Make sure to frequently check and calibrate the settings for optimal performance based on the job requirements.
The Future of MIG Welding for Electricity Suppliers
The MIG 250 welding machine symbolizes a shift towards more efficient and adaptable technology in the welding field. As electricity suppliers continue to evolve, the demands for high-quality, reliable welding solutions will increase. The MIG 250 stands at the forefront, offering features and specifications that are becoming essential in the rapidly changing landscape of electrical supply.
Investing in the MIG 250 not only enhances productivity but also ensures that electricity suppliers maintain high-quality standards in their operations. As technology advances, suppliers must stay abreast of the latest in welding technology to ensure they remain competitive.
For further information, tips, and inquiries about the MIG 250 and its applications, visit Allure.com.ua.