CNC Lathe Machine Parts Name: A Comprehensive Guide for Metal Fabricators
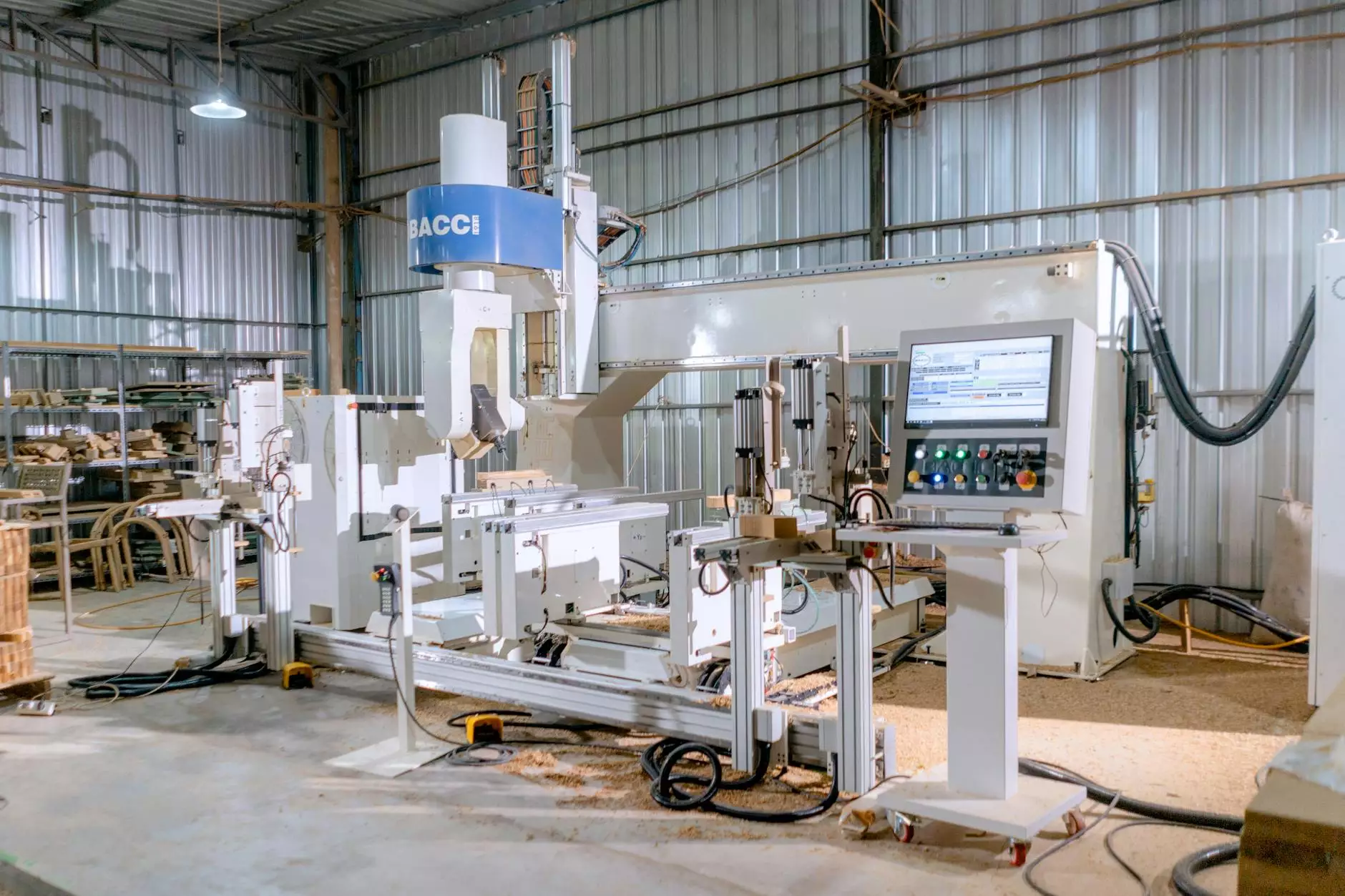
CNC (Computer Numerical Control) lathes are pivotal in modern manufacturing, especially in the realm of metal fabrication. Understanding the various CNC lathe machine parts names and their respective functions is essential for operators, designers, and engineers alike. This detailed guide will navigate through the fundamental components of CNC lathes, shedding light on their functionalities and significance within the fabricating industry.
Understanding CNC Lathes
CNC lathes represent a critical advancement in machining technology. These sophisticated machines automate the precision turning of materials, which is crucial in producing parts with intricate designs. By comprehending the parts of CNC lathes, you will gain insight into how these machines can optimize production processes and improve overall efficiency.
Key Components of CNC Lathes
The operation of a CNC lathe is dependent on numerous parts working cohesively. Below is a detailed exploration of significant CNC lathe machine parts names and their typical functions:
#1. Headstock
The headstock is often regarded as the heart of the CNC lathe. It houses the primary components responsible for driving and controlling the workpiece's rotation.
- Spindle: A cylindrical structure rotating the workpiece. The spindle's speed and torque are adjustable to suit various machining requirements.
- Gearbox: Transmits motor power to the spindle and allows for the adjustment of spindle speed.
- Chuck: A clamping device that securely holds the workpiece in place as it rotates.
#2. Tailstock
The tailstock serves multiple purposes, particularly supporting long workpieces and providing alignment:
- Live Center: A precision component that rotates with the workpiece, maintaining support without impeding movement.
- Quill: An adjustable part that allows for positioning of the live center or tools and accommodates various material lengths.
#3. Bed
The bed of the CNC lathe is the foundational structure that provides stability and support to other components:
- Guide Rails: Ensures linear motion of the carriage and cross-slide, enabling precise cuts and shapes.
- Base Frame: Provides stability and absorbs vibrations, crucial for precision engineering.
#4. Carriage
The carriage is integral to the longitudinal movement of cutting tools:
- Cross-Slide: Allows for lateral movement, enabling the tool to cut across the workpiece.
- Apron: Houses the controls and mechanisms for the movement of the carriage.
#5. Control Panel
The control panel is the interface for the operator, allowing input of machining parameters:
- Display Screen: Provides real-time feedback and information regarding the machining process.
- Button Interface: Facilitates easy operation and setting adjustments for the user.
#6. Tool Holder
The tool holder secures the cutting tools and enables different operations:
- Tool Post: Adjusts the position of the tool for different cutting angles.
- Indexable Inserts: Replaceable cutting tips that allow for flexibility in machining different materials.
#7. Chips Conveyor
The efficient removal of metal chips and swarf is handled by the chips conveyor, which aids in maintaining clean working conditions and helps prolong machine life.
Types of CNC Lathe Machines
Understanding the types of CNC lathes can further enhance your comprehension of their applications in the industry. Here are several prominent types:
- Horizontal CNC Lathe: The most common type, featuring a horizontal bed and suitable for various machining tasks.
- Vertical CNC Lathe: Ideal for large and heavy workpieces, providing enhanced stability.
- Swiss CNC Lathe: Employed for high-precision manufacturing, particularly in small-diameter parts.
- Multi-tasking CNC Lathes: Combine turning, milling, and drilling capabilities for versatile machining solutions.
Applications of CNC Lathe Machines in Metal Fabrication
CNC lathes are widely utilized across various industries for different applications. Some common uses include:
- Automotive Components: Manufacturing of gears, shafts, and intricate parts.
- Aerospace Parts: Creation of lightweight components with stringent precision requirements.
- Medical Devices: Production of precision instruments and implants.
- Electronics: Fabrication of small parts such as connectors and housings.
Benefits of CNC Lathes in Manufacturing
The advantages of employing CNC lathe machines extend beyond mere precision:
- Increased Productivity: Automation allows for faster production rates, significantly reducing lead times.
- Consistency and Quality: CNC machines produce identical parts with minimal deviation, enhancing overall quality control.
- Complex Geometries: Ability to program intricate shapes that are challenging to achieve with manual lathes.
- Reduced Need for Skilled Labor: Operators need less expertise compared to manual lathes, as CNC machines handle the complex tasks.
Factors to Consider When Choosing a CNC Lathe
Selecting the right CNC lathe machine for your operations involves evaluating several key factors:
- Workpiece Size: Determine the maximum length and diameter of the parts you intend to fabricate.
- Material Types: Ensure the machine can handle the materials, such as aluminum, steel, or titanium.
- Precision Needs: Choose a machine that meets the tolerances required for your products.
- Budget: Establish a budget while considering the total cost of ownership, including maintenance and operation.
Conclusion
In summary, the exploration of CNC lathe machine parts names provides valuable insight for anyone involved in metal fabrication. Understanding each component's role not only enhances operational efficiency but also contributes to a higher quality of finished products. As the industry moves towards increasing automation and precision, the knowledge of CNC lathe parts and their functionality will remain a crucial aspect of success for metal fabricators. For more detailed information and products related to metal fabrication, visit deepmould.net.