Exploring the World of Custom Plastic Molding in China
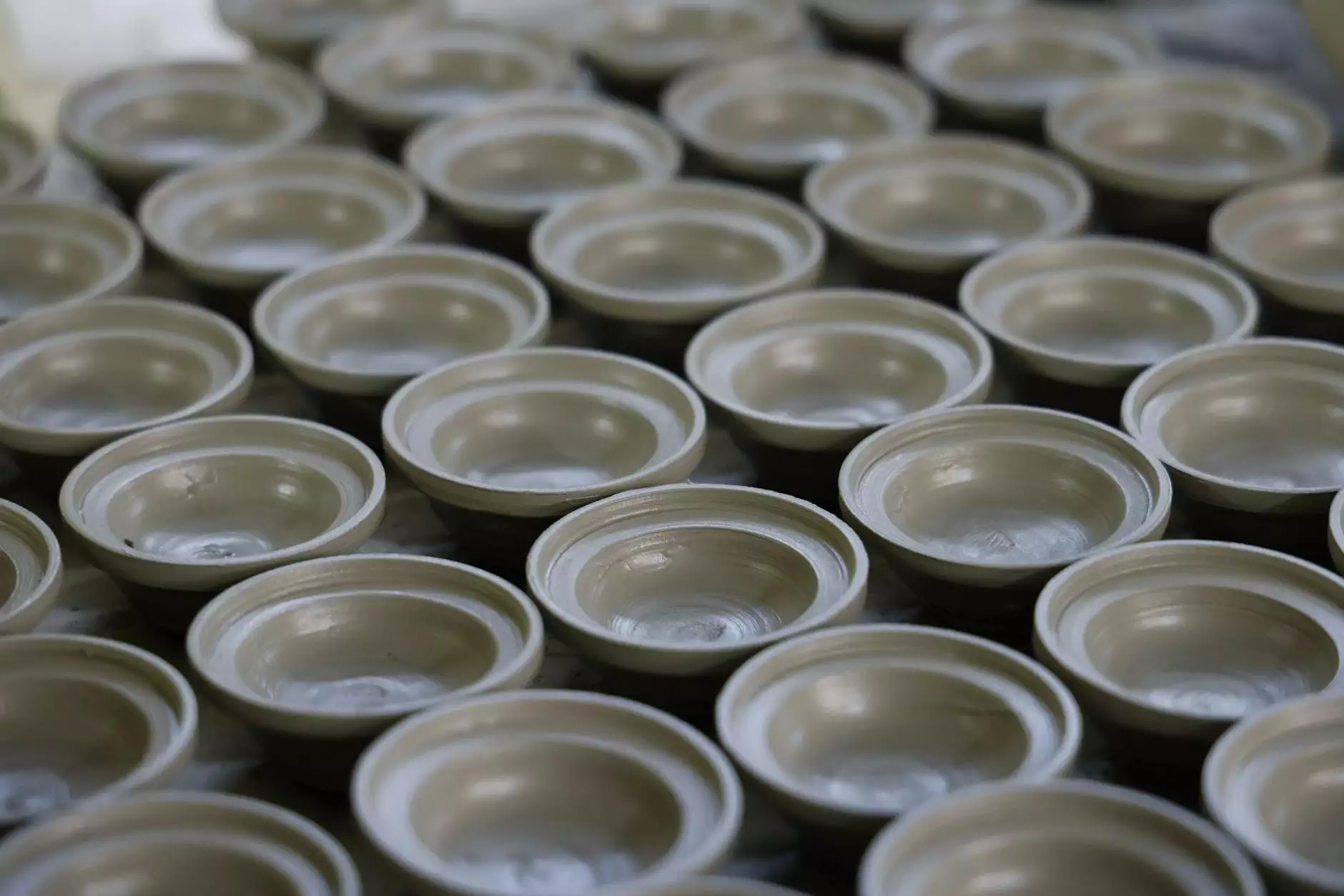
In today’s fast-paced manufacturing landscape, custom plastic molding in China has emerged as a critical component for businesses looking to create high-quality plastic products efficiently and economically. This article delves into the intricacies of plastic mold making and injection molding, highlighting the significant advantages of partnering with reputable manufacturers like Hanking Mould.
Understanding Custom Plastic Molding
Custom plastic molding is a manufacturing process used to produce plastic parts and products that meet specific requirements. This technique is pivotal for a variety of industries, including automotive, electronics, consumer goods, and medical applications. The essence of this process lies in its ability to create complex shapes and designs while maintaining precision and efficiency.
Types of Custom Plastic Molding Processes
Several methods are employed in the realm of custom plastic molding. Let’s explore the most prevalent techniques:
- Injection Molding: This process involves injecting molten plastic into a mold cavity. It is ideal for mass production and can produce a variety of shapes rapidly.
- Blow Molding: Typically used for creating hollow plastic products, this method involves inflating a hot plastic tube to form a shape against the mold.
- Rotational Molding: In this method, a powdered plastic is placed into a mold, which is then heated and rotated to achieve a consistent thickness across the product.
- Thermoforming: This technique involves heating a plastic sheet until pliable and then forming it over a mold. It is often used for creating packaging and large parts.
Advantages of Custom Plastic Molding in China
The choice of China as a destination for custom plastic molding comes with a plethora of advantages:
Cost-Effectiveness
One of the most compelling reasons for outsourcing plastic molding to China is the significant cost savings. China’s robust manufacturing infrastructure, skilled workforce, and competitive labor rates translate into lower production costs without compromising quality.
Access to Advanced Technologies
China has made tremendous strides in technological advancement, utilizing state-of-the-art equipment to enhance production efficiencies and product quality. Companies like Hanking Mould leverage modern technologies to deliver precise and complex molds.
Rapid Turnaround Time
In bustling markets where time-to-market is critical, China’s manufacturers offer rapid prototyping and short lead times. This flexibility enables businesses to adapt quickly to changing market demands and consumer preferences.
Quality Assurance
With international standards increasingly being adopted, Chinese manufacturers are committed to quality assurance processes. By opting for custom plastic molding in China, companies can benefit from rigorous quality control at every stage of production.
Key Considerations When Choosing a Plastic Mold Maker
When selecting a plastic mold maker in China, several factors must be considered to ensure you receive the best possible service and product quality:
Experience and Expertise
Verify the experience of the mold maker. A company like Hanking Mould, with years of experience in the industry, is well-equipped to handle diverse project requirements.
Technological Capabilities
Assess the technologies employed by the manufacturer. Advanced machinery and techniques can significantly impact the quality and efficiency of the production process.
Customization Options
Ensure that the mold maker offers comprehensive customization options that cater to your specific product needs. Flexibility in design changes and adaptations is vital for achieving the desired outcomes.
Reviews and Feedback
Research feedback from previous clients. Positive reviews and strong testimonials can provide insight into the reliability and quality of the mold maker’s services.
Plastic Injection Mould Manufacturer: Hanking Mould
Hanking Mould stands out as a premier plastic injection mould manufacturer, known for its commitment to quality, innovation, and customer satisfaction. With a mission to deliver unparalleled service, Hanking Mould operates with the following principles:
Customization and Flexibility
At Hanking Mould, customization is at the forefront. They understand that every client has unique needs, and they work closely with businesses to design molds that meet specific project requirements.
Expert Team
The team at Hanking Mould comprises experienced professionals dedicated to each project. From design to production, their expertise ensures that every mold meets the highest standards of quality and precision.
Commitment to Sustainability
Hanking Mould is also committed to sustainable practices. They utilize eco-friendly materials and processes, ensuring that their manufacturing not only meets industry standards but also contributes positively to the environment.
The Process of Custom Plastic Molding
Engaging in custom plastic molding typically involves several steps:
1. Design and Prototyping
The first step in the process is creating a design that outlines the specifications and dimensions of the product. This may involve CAD (Computer-Aided Design) software to visualize the product. Following the design, prototyping allows for testing and refinement before the molding process begins.
2. Mold Creation
Once the design is finalized, the next stage involves creating the mold. This is a critical step, as the mold dictates the final product’s shape and quality. Advanced CNC machining techniques are often used to achieve precision.
3. Injection and Cooling
After the mold is prepared, the next step involves injecting molten plastic into the mold cavity under high pressure. Once filled, the product is allowed to cool and solidify, taking the shape of the mold.
4. Finishing Touches
Post-cooling, the product undergoes finishing processes, which may include trimming, surface treatment, or painting to meet the aesthetic and functional requirements.
5. Quality Control
Finally, rigorous quality control measures are implemented to ensure that the final product meets all specifications and standards before it is delivered to the client.
Future Trends in Custom Plastic Molding
The landscape of custom plastic molding is continually evolving. Key trends to watch include:
Innovation in Materials
The demand for bio-based and sustainable materials is rising. Manufacturers are investing in R&D to develop new materials that are not only more environmentally friendly but also competitive in performance.
Advanced Manufacturing Techniques
Technological innovations, such as automation and smart manufacturing practices, are transforming production processes. These advancements enhance efficiency, reduce waste, and improve overall product quality.
Increased Customization
As consumer preferences continue to shift towards personalization, manufacturers are focusing on providing highly customizable solutions to meet the specific needs of different markets.
Conclusion: Partnering for Success
In conclusion, custom plastic molding in China offers significant benefits, from cost savings to advanced technological capabilities. By partnering with a reputable manufacturer like Hanking Mould, businesses can ensure high-quality plastic products tailored to their specifications. The future of manufacturing is bright, and those who adapt to evolving technologies and consumer demands will thrive in this competitive landscape.
If you’re looking to enter the world of custom plastic molding or require expert services in plastic injection molding, contact Hanking Mould today to discuss your project and discover how they can help elevate your business production capabilities.
custom plastic molding china